该工艺是以无缝管为管坯, 感应加热, 芯棒导向、推挤成形的弯头生产方法, 能生产各种小角度弯头和符合美国(ANSI)、德国(DIN)、日本(JIS)、国际标准(ISO)的45°、90°、180°的弯头。
(1)推挤原理
如图3-1所示, 根据每种弯头所需的管料长度, 将管坯6集中套装在导向芯棒3上, 芯棒用插板与机架2固定。推板4(由丝杠5带动)推动管坯向前移动, 管坯在到达感应加热线圈7后开始加热, 加热温度850~950℃, 然后在推板的轴向推力作用和导向芯棒的导向下, 逐渐变形使管坯扩孔弯曲, 一次成形。成形后的管弯头在后续的推动下, 脱离导向芯棒进行下道工序。
1.同步调速减速器;2.机架;3.导向芯棒;4.推板;5.丝杠;6.管坯;7.感应加热线圈。
(2)工艺优点
a)保证弯头各截面壁厚均匀
由于管坯各截面加热均匀, 在芯棒导向扩孔弯曲时与芯棒整体接触, 故不存在管坯局部温度下降, 亦即管坯各部位不存在塑性好坏之分, 也不存在加工硬化现象, 使管坯在很好的条件下产生热塑性变形一扩孔弯曲, 保证弯头各截面壁厚均匀, 达到标准要求, 避免了在传统的外接触弯模中出现的壁厚不均的缺陷。
b)确保内孔尺寸和圆度要求
弯头内孔是在芯棒导向下扩孔成形的, 其内孔尺寸由芯棒的截面形状及尺寸决定,故可以方便地避免在传统的弯管工艺中出现的由于管壁强度不足而使截面失圆的缺陷。
c)能生产各种小角度弯头和高标准的弯头
由于管坯塑性变形均匀、无加工硬化现象及芯棒导向扩孔弯曲成形, 避免了在传统的冷弯成形和热弯成形工艺中壁厚不均、截面失圆的缺陷, 可以生产各种小角度弯头和高标准的弯头。
(3)工艺要点
a)芯棒形状及几何尺寸要求(见图3-2)
芯棒分为杆部和头部两部分。杆部材料为热轧圆钢, 外圆尺寸比管坯内孔略小头部为铸造耐热模具钢,其弯曲半径为弯头的弯曲半径, 外径渐大, 头部直径等于弯头内孔直径。两部分通过焊接而成。
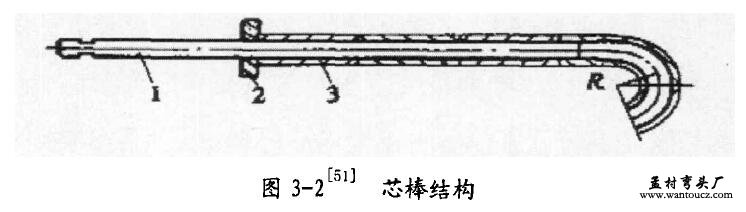
1.芯棒;2.推板;3.管坯
b)加热速度和推挤速度
加热与推挤同步进行, 加热速度必须与推挤速度相适应。如加热速度过快, 则会出现管坯过热、过烧的缺陷, 使弯头质量下降或报废, 如推挤速度过快, 则会出现塑性不足, 推力过大, 使扩孔弯曲成形困难, 甚至拉断芯棒和损坏弯管机。
c)推挤前芯棒预加热
在第一只弯头推挤前必须先将芯棒头扩孔弯曲部分预加热, 约800℃左右, 否则, 加热后的第一只管坯在前进至芯棒的扩孔弯曲部分时温度骤降, 管坯的收缩应力和塑性下降使推挤力增大, 管坯变形困难, 推挤难以进行。此后的加工中由于推挤连续进行, 芯棒头温度会同管坯的温度保持一致, 无需加热。因此, 芯棒头扩孔弯曲部分预加热只须在弯管机停息后重新加工或芯棒换过后才进行。
d)管坯内涂敷高温固体润滑剂
在推挤过程中, 管坯内孔与芯棒外圆表面紧密接触, 同时, 加热后塑性加大, 管坯内孔与芯棒外圆表面间的摩擦力增大, 必须在管坯内壁涂敷高温固体润滑剂进行润滑,否则会使弯头内孔粗糙或推挤无法进行。
e)管坯尺寸
虽然管坯在弯曲时孔径的扩大对保证弯头管壁厚度公差有利, 但对管坯的选材有不同的要求。一般选择与弯头管壁厚相等、外圆尺寸小一规格的无缝管作为管坯。当弯头壁厚与无缝管坯稍有差异时, 可调节推挤速度来保证管壁厚度。